BMW satsar stort på att elektrifiera bilflottan med sin nya “Neue Klasse”-plattform, där högspänningsbatteriet är en avgörande del.
BMWs framtid: Batteriet får ny roll i bilens bärande struktur
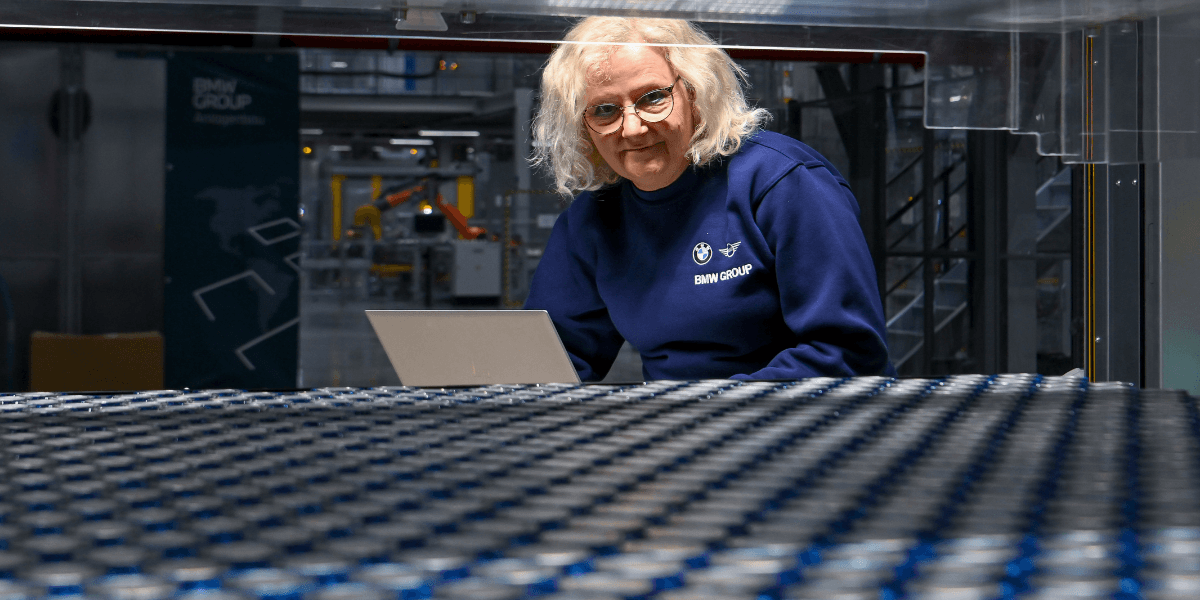

Mest läst i kategorin
För att allt ska flyta smidigt när den storskaliga produktionen drar igång, utvecklas och testas tillverkningsprocesserna noggrant. Detta sker i toppmoderna pilotanläggningar i Parsdorf, Hallbergmoos och i forsknings- och innovationscentret (FIZ) i München.
Denna satsning i Tyskland stärker inte bara landets förmåga att innovera, utan lägger också grunden för att batteriproduktionen ska kunna rullas ut över hela världen med högsta möjliga kvalitet och effektivitet, skriver BMW.
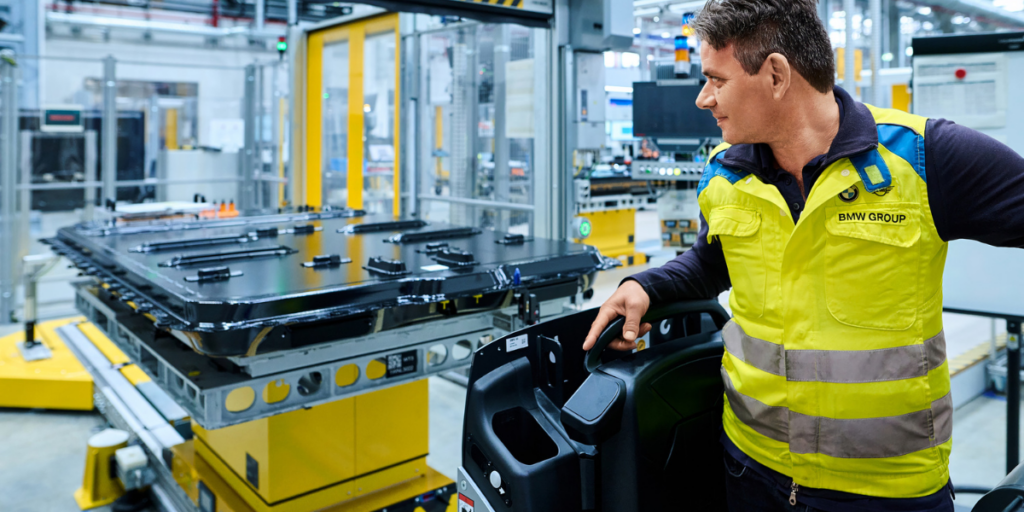
Kvalitet i fokus med nollfelsstrategi
BMW Group har en ambitiös nollfelsstrategi för tillverkningen av det egenutvecklade högspänningsbatteriet Gen6.
Markus Fallböhmer, chef för batteriproduktion på BMW AG, förklarar vikten av detta:
“För produktionen av våra högspänningsbatterier eftersträvar vi en konsekvent nollfelsstrategi. Högintelligenta, AI-stödda kvalitetskontroller är integrerade i produktionsprocessen för att hjälpa oss att uppnå detta”.
Kvaliteten är avgörande eftersom högspänningsbatteriet i “Neue Klasse”-modellerna fungerar som en bärande del i bilens kaross, ett koncept som kallas ‘pack to open body’. De nya cylindriska cellerna integreras direkt i högspänningsbatteriet, en metod kallad ‘cell to pack’.
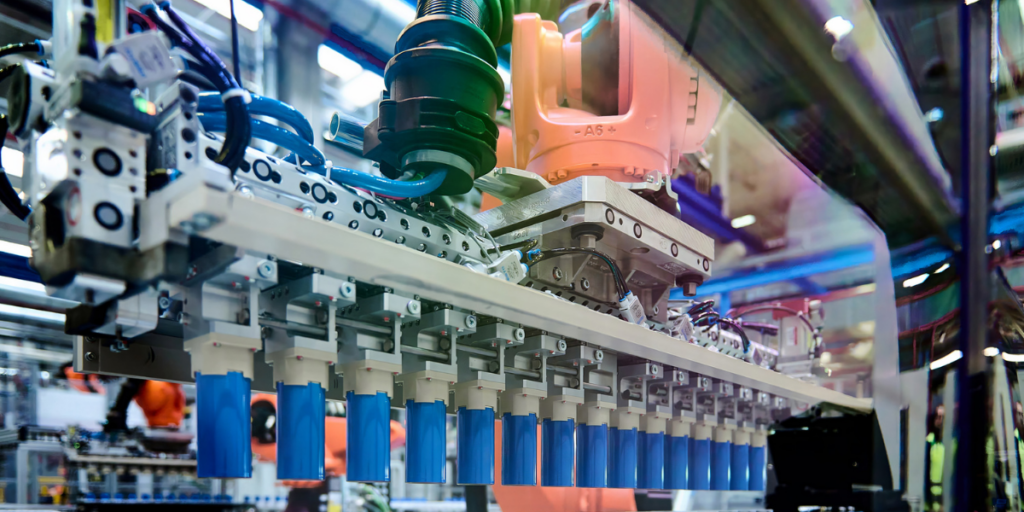
BMW Groups pilot- och serieanläggningar sätter nya standarder för batteriproduktion tack vare innovativa processer. Exempelvis används digitala produktionstvillingar för att träna personal och avancerade AI-databaser för att optimera logistiken.
Alla produktionssteg övervakas konstant för att säkerställa maximal stabilitet och kontinuerlig, databaserad optimering.
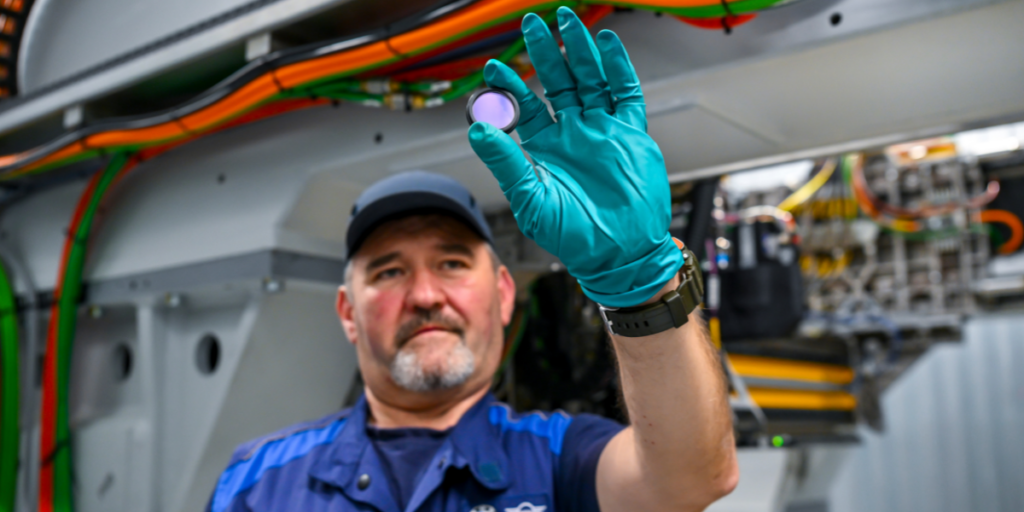
Senaste nytt
Pilotanläggningarna i Bayern driver utvecklingen
De bayerska pilotanläggningarna är navet i BMW Groups satsning på nya högspänningsbatterier. Den största pilotanläggningen för Gen6-batterier ligger i Parsdorf, där över 350 anställda har byggt de första prototyperna sedan 2023.
Sedan mitten av 2024 har en del av dessa batterier skickats till fordonsfabriken i Debrecen, Ungern, för att installeras i testfordon för “Neue Klasse”.
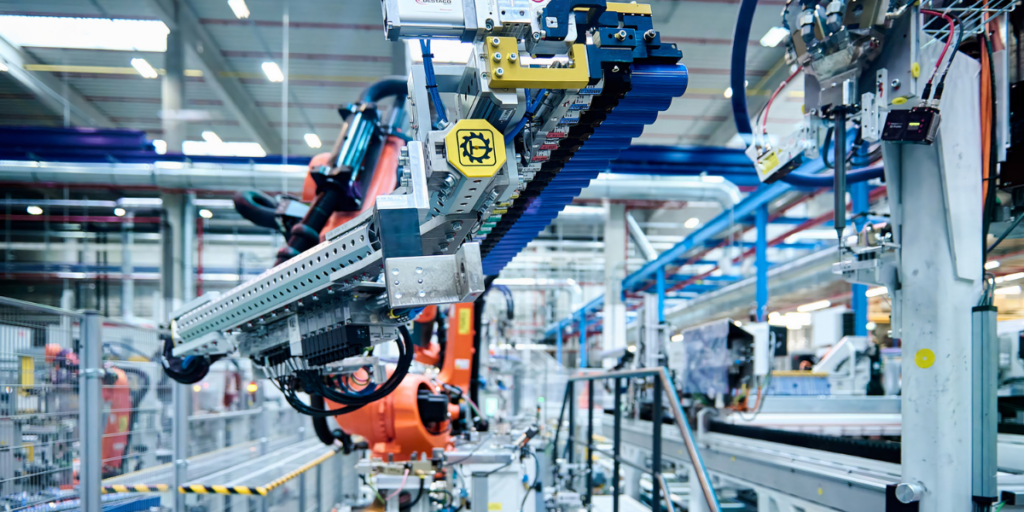
En annan anläggning för förserieproduktion av högspänningsbatterier finns nära Münchens flygplats, i Hallbergmoos. Sedan sommaren 2024 har cirka 200 anställda där utvecklat tillverkningstekniker för montering av högspänningsbatterier.
Denna anläggning fungerar som en förebild för serieproduktionen vid fabriken i Woodruff, nära Spartanburg i USA. Dessutom tillverkar och testar ytterligare 200 anställda prototyper och mindre modulvarianter av högspänningsbatteriet vid Münchens forsknings- och innovationscenter (FIZ), närmare bestämt i det nyöppnade Aeroacoustics and E-drive Centre (AEZ).
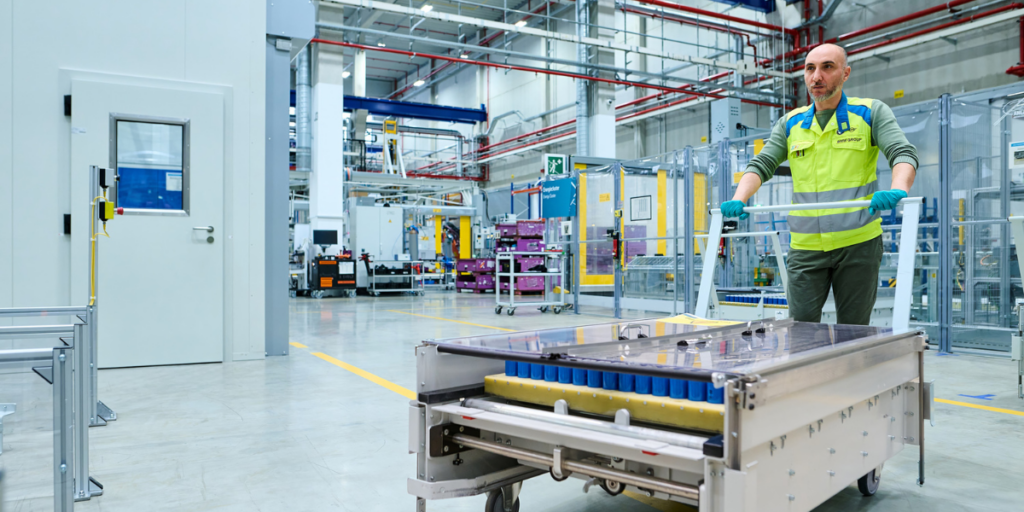
Global utrullning på kort tid
Systemen och processerna som utvecklats vid de bayerska pilotanläggningarna kommer att implementeras globalt. Inom mindre än två år kommer serieproduktionen att starta vid fem anläggningar på tre kontinenter.
BMW Group följer sin princip om ‘local-for-local’, vilket innebär att anläggningarna för Gen6 högspänningsbatterier placeras så nära bilfabrikerna som möjligt. Detta skyddar produktionen mot oväntade politiska och ekonomiska händelser, samtidigt som befintliga produktionsplatser stärks och nya jobb skapas.
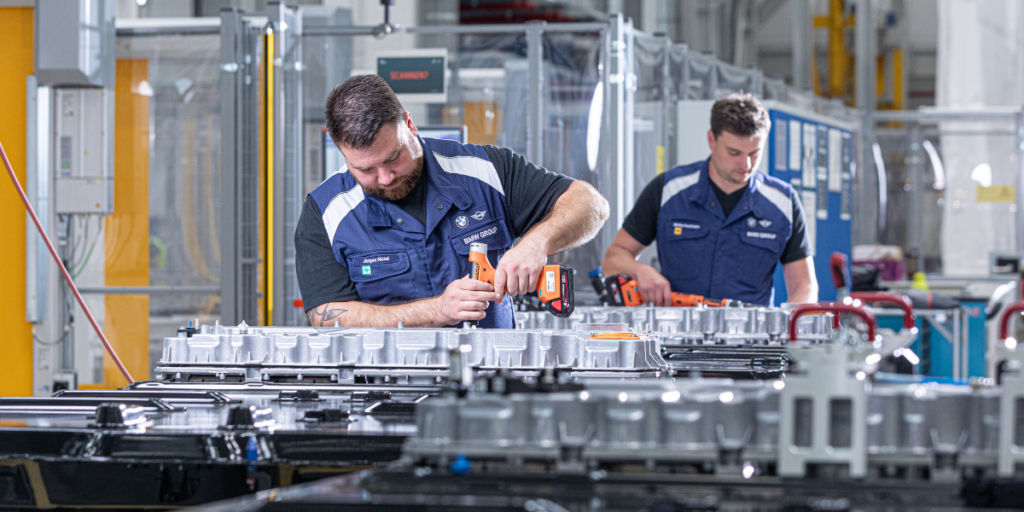
Serieproduktionen av BMW iX3, den första modellen i “Neue Klasse”, börjar i Debrecen i slutet av 2025, samtidigt som tillverkningen av högspänningsbatterier på samma plats. Efter Debrecen följer batterimonteringsfabrikerna i Shenyang (Kina), Irlbach-Straßkirchen (Bayern), Woodruff (USA) och San Luis Potosí (Mexiko).
Hur BMW bygger Gen6 högspänningsbatterier
BMW Group köper in battericeller till sina högspänningsbatterier från ledande tillverkare, som producerar cellerna enligt BMWs höga tekniska krav. När cellerna tas emot, utförs extra kontroller, som spänningsmätningar.
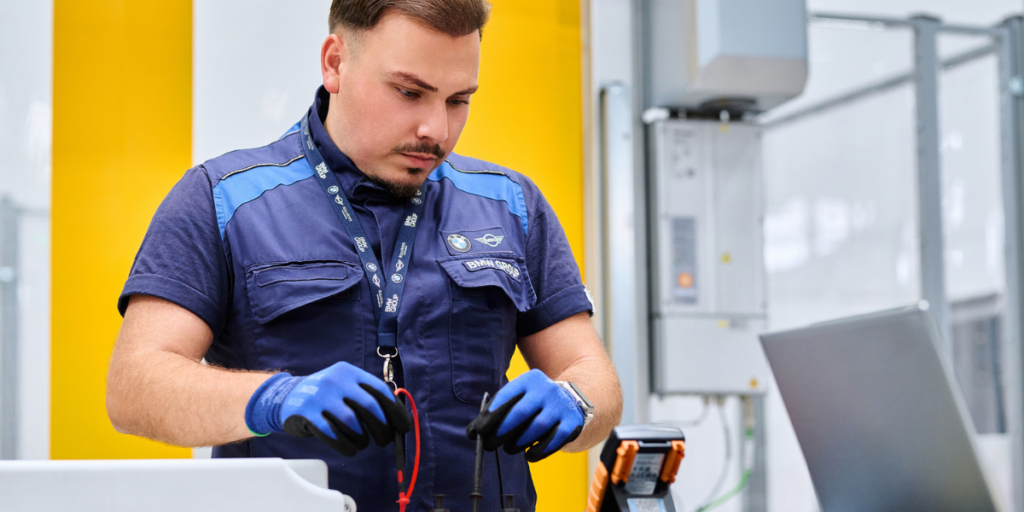
Nästa steg är cellklustring, där battericellerna ansluts till ett kylsystem för optimal isolering och kylning. Sedan rengörs och svetsas cellkluster och cellkontaktsystem precisionsmässigt med laser, med konstant övervakning i realtid. Därefter följer en innovativ skumprocess som skyddar alla delar som en mekanisk enhet, vilket garanterar högspänningsbatteriets säkerhet, stabilitet och hållbarhet. Höljet stängs, förseglas och nitas.
I sista steget monteras Energy Master – den centrala styrenheten – på högspänningsbatteriet med ett permanent elastiskt tätningslim. Slutligen genomgår varje högspänningsbatteri en hundraprocentig slutkontroll för att garantera kvalitet, säkerhet och funktion.
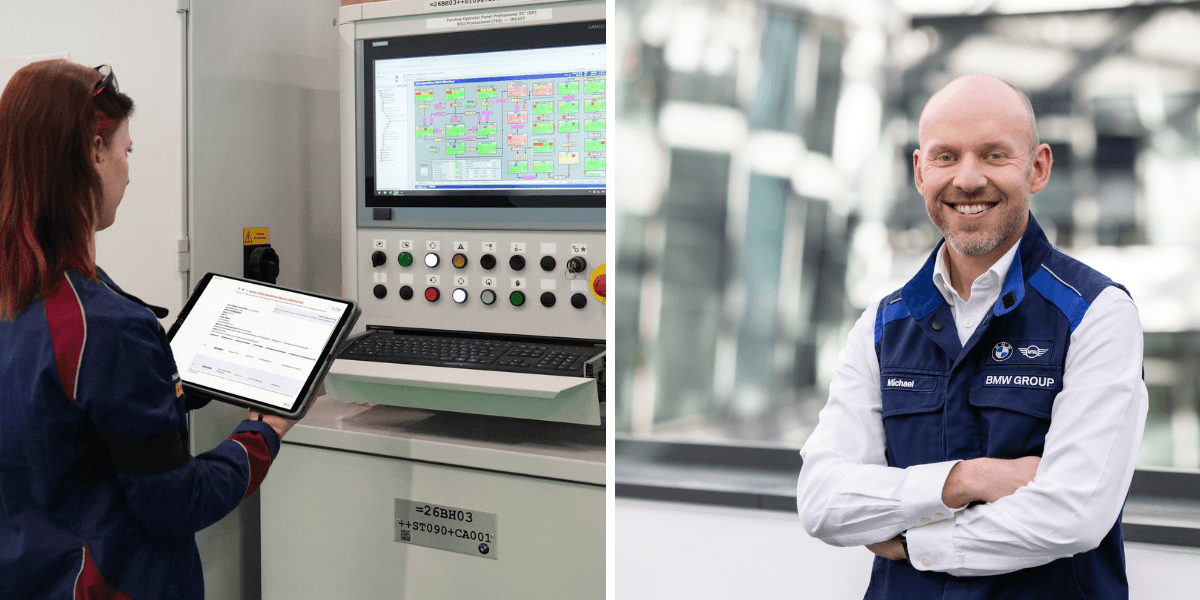
AI räddar produktionslinjen – här är BMW:s nya hjälte
BMW introducerar AI-assistenten Factory Genius, som hjälper till att effektivisera underhåll och felsökning i produktionen. I en tid där varje minut
Missa inte:
Skatteverket ser oroande trend – få redovisar kryptohandel. News 55
Pensions-varningen: Då ska du inte byta jobb efter 50 års ålder. E55
Fastighetsägare väljer tomma lokaler framför hyresintäkter. Realtid

Åsa Wallenrud är en driven och erfaren motorjournalist med en stark passion för bilvärlden och teknik, gärna i kombination. Arbetat med varumärken som TV4 Nyhetsmorgon, Facit, M3, Lilla Gumman, Hem och Villamässor, Blocket, Byt Bil mfl. Har du en bra historia? Maila mig [email protected]

Åsa Wallenrud är en driven och erfaren motorjournalist med en stark passion för bilvärlden och teknik, gärna i kombination. Arbetat med varumärken som TV4 Nyhetsmorgon, Facit, M3, Lilla Gumman, Hem och Villamässor, Blocket, Byt Bil mfl. Har du en bra historia? Maila mig [email protected]